Технология ультразвукового контроля сварных соединений стенки стальных вертикальных резервуаров без удаления защитного лакокрасочного покрытия
ПРЕДИСЛОВИЕ 2022 г.
Данная статья с незначительными сокращениями опубликована в журнале «Трубопроводный транспорт: теория и практика» (2008 г. №11). Технология ультразвукового контроля через антикоррозионное покрытие разработана в 2006 г. в ЗАО «ВНИИСТ-Диагностика», подготовлен и внедрен руководящий документ ОАО «АО «Транснефть» РД-19.100.00-КТН-545-06 «Ультразвуковой контроль стенки и сварных соединений при эксплуатации и ремонте стальных вертикальных резервуаров» ( в 2018 г. заменен на РД-19.100.00-КТН-005-18 «Магистральный трубопроводный транспорт нефти и нефтепродуктов. Техническое диагностирование резервуаров. Неразрушающий контроль внутренних металлоконструкций резервуара без удаления антикоррозионного покрытия»).
По результатам работы, проведенной в 2006 г. были получены общие характеристики прохождения ультразвука для различных групп (полиуретановые; эпоксидные и полиуретановые; эпоксидные и кремнийорганические; эпоксидные и акрил – полиуретановые; эпоксидные и винил – эпоксидные; винил – эпоксидные) антикоррозионных покрытий. Предполагалось, что данные, полученные для групп, можно будет распространить на конкретные марки покрытий. В настоящее время стало ясно, что такой подход не дает корректных результатов и поправочные коэффициенты следует определять для каждого конкретного типа антикоррозионного типа.
ООО «НИИЦ СТНК «Спектр», где в настоящее время работают авторы статьи, обладает методикой и оборудованием для определения поправок к чувствительности ультразвукового контроля эхо-методом через антикоррозионное лакокрасочное покрытие и методикой выполнения ультразвукового контроля через покрытие. Технология УЗК может быть распространена на контроль с применением преобразователей с фазированными решетками. Влияние антикоррозионного покрытия на результаты контроля TOFD методом требуют изучения: вследствие влияния покрытия глубина верхней мертвой зоны увеличивается.
The procedure of ultrasonic testing of steel oil storage tanks welded joints without removing the protective paint and varnish coating
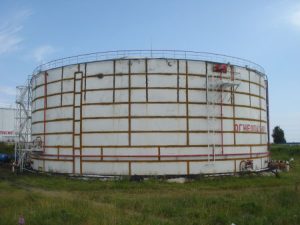
При техническом диагностировании стальных резервуаров в процессе эксплуатации обязательным является проведение ультразвукового контроля основного металла и сварных соединений. Поверхность резервуаров имеет антикоррозионное лакокрасочное покрытие, которое в соответствии с традиционным подходом, должно быть удалено для проведения УЗ контроля.
Необходимость удаления защитного покрытия обусловлена его влиянием на выявляемость дефектов. Интерференция ультразвука в слое покрытия переменной толщины приводит к осцилляциям чувствительности и, как следствие, неверной оценке амплитуды эхо-сигнала от несплошности в металле, к недобраковке критических дефектов или перебраковке допустимых дефектов.
Удаление и восстановление защитного покрытия после контроля требует значительных материальных затрат и организационных усилий с привлечением специализированных организаций. При применении традиционной технологии УЗ контроля сварных швов и металла стенки резервуара расходы на подготовку (зачистку) поверхности к контролю и на восстановление защитного покрытия резервуара для хранения нефти объемом 20000 м³ могут достигать 4-6 % от первоначальной стоимости резервуара.
Применение современных лакокрасочных материалов гарантирует защиту резервуара от коррозии в течение 15-20 лет, а нормативные документы (например, РД-16.01-60.30.00-КТН-063-1-05 ОАО «АК «Транснефть») регламентируют выполнение диагностики с периодичностью 4 – 5 лет. В этих условиях возникают вопросы: как проводить техническую диагностику резервуаров, имеющих гарантию по покрытию? Можно ли обеспечить полноценный УЗ контроль без удаления антикоррозионного покрытия, находящегося на гарантии?
Для ответа на эти вопросы выполнены экспериментальные исследования влияния лакокрасочного покрытия на параметры ультразвукового контроля (чувствительность, угол ввода) в зависимости от типа и толщины покрытия.
Номенклатура применяемых лакокрасочных покрытий весьма широка. Поэтому в ходе исследований все покрытия были разбиты на семь групп в зависимости от основы используемых лакокрасочных материалов:
- полиуретановые (STEELPAINT, E WOOD);
- эпоксидные и полиуретановые (AMERON, HEMPEL, JOTUN, International Protective Coatings);
- эпоксидные и кремнийорганические (ВГ-33 + КО-814);
- эпоксидные и акрил – полиуретановые (PERMATEX);
- эпоксидные и винил – эпоксидные (Виникор – цинк ЭП-057);
- винил – эпоксидные (Виникор-62);
- полиуретановые и акрил – полиуретановые (в т.ч.: УР0446 (бывший УР0432).
В ходе экспериментов выяснено как толщина антикоррозионного покрытия влияет на выявляемость дефектов металла стенки РВС. Исследования выполнены на представительной выборке покрытий по их типам и основам.
На рисунке 2 представлен пример результатов экспериментальных исследований влияния толщины и типа лакокрасочного покрытия на чувствительность контроля, полученных для частоты 5.0 МГц и угла ввода 60 градусов (для случая сдвиговой волны). Полученные зависимости позволяют выполнить корректировку чувствительности дефектоскопа при контроле сварных швов и металла резервуара. Аналогичные зависимости получены для углов ввода 45, 70 градусов и соответствующих частот ультразвуковых колебаний 2.5, 5.0 МГц.
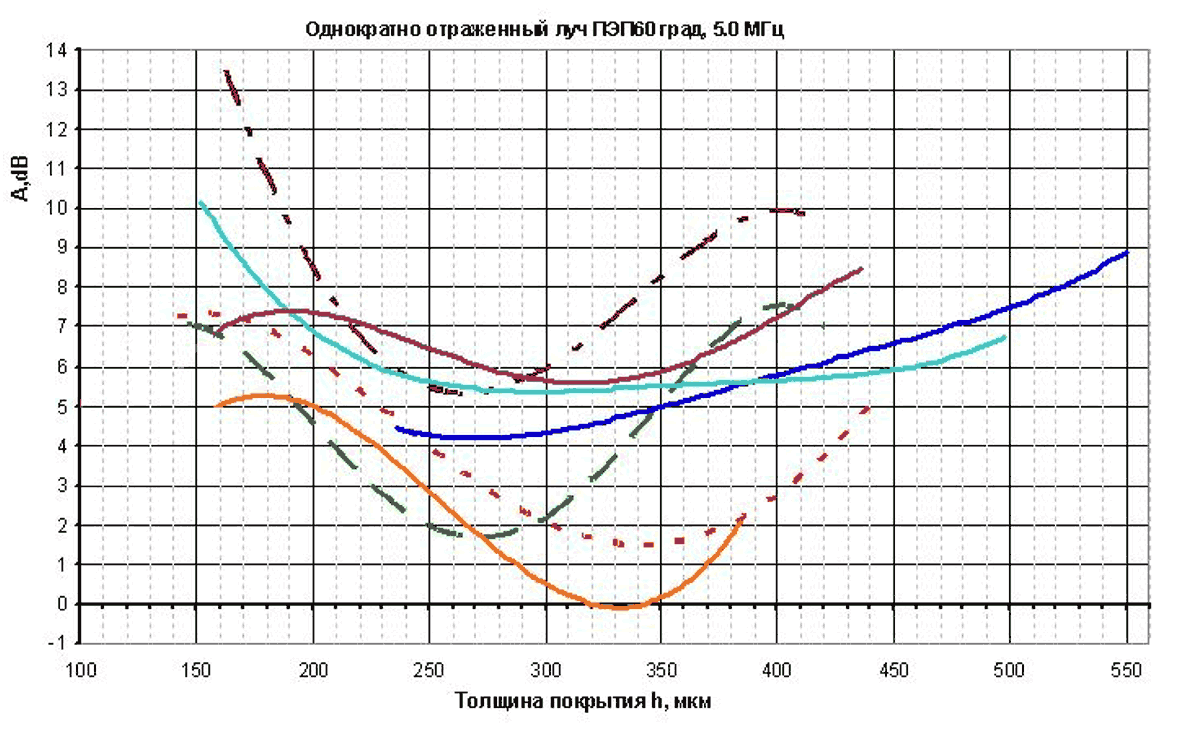
Эти и подобные полученные зависимости позволили выработать подход к УЗ контролю стенки без удаления антикоррозионного покрытия. Основой этого подхода является выбор таких параметров контроля, при которых влияние толщины покрытия минимально, и ввод ряда поправочных коэффициентов, учитывающих свойства покрытия.
Контроль сварных соединений через антикоррозионное покрытие выполняется за 4 этапа, в последовательности, показанной на рисунке 3.

1-й этап: выполняется визуальный и измерительный контроль сварного соединения, антикоррозионного покрытия в зоне перемещения пьезоэлектрического преобразователя (ПЭП).
2-й этап: выполняется УЗК при чувствительности, повышенной, на 6-10 дБ.
3-й этап: измеряется толщина антикоррозионного покрытия в зоне расположения ПЭП при обнаружении дефекта.
4-й этап: корректируются результаты УЗК (амплитуда сигнала и условной протяженности) в зависимости от толщины и вида покрытия.
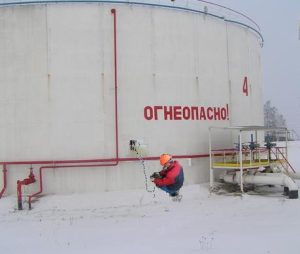
стенки резервуара без удаления
антикоррозионного покрытия
Описанная выше технологическая процедура УЗ контроля сварных швов стенки резервуара реализуется с применением любого ультразвукового дефектоскопа общего назначения, имеющего в своем комплекте стандартные пьезоэлектрические преобразователи с углами ввода 45, 60, 70 градусов с рабочей частотой 2.5 и 5.0 МГц.
Данная технология явилась основой разработанного норматива РД-19.100.00-КТН-545-06 «Ультразвуковой контроль стенки и сварных соединений при эксплуатации и ремонте стальных вертикальных резервуаров» и внедрена в системе ОАО «АК «Транснефть».
Сведения об авторах на 2009 г:
- Леонид Юрьевич Могильнер, кандидат технических наук, генеральный директор ЗАО «ВНИИСТ-Диагностика», Москва.
- Иван Петрович Литвинов, начальник Отдела разработки технологий и оборудования, ЗАО «ВНИИСТ-Диагностика», Москва.
- Денис Викторович Окунев, главный специалист Отдела разработки технологий и оборудования, ЗАО «ВНИИСТ-Диагностика», Москва.
Ключевые слова: УЗК, ультразвуковой контроль через лакокрасочное покрытие, антикоррозионное покрытие
-
Технология ультразвукового контроля сварных соединений стенки стальных вертикальных резервуаров без удаления защитного лакокрасочного покрытия
В статье описана технология проведения квалификационных испытаний средств неразрушаю-щего контроля стыковых кольцевых сварных соединений трубопроводов позволяющая снизить стоимость испытаний и сократить их сроки. Предложена система классификации установок ультра-звукового контроля по функциональным возможностям.
02/10/2008 Далее -
Технология проведения квалификационных испытаний средств неразрушающего контроля. Классификация средств ультразвукового контроля
Задачей квалификационных испытаний является определение реальных возможностей установок неразрушающего контроля (далее –НК) по выявлению дефектов, расчёт ошибок измерения размеров дефектов
12/09/2015 Далее -
Оценка результатов валидации установок АУЗК
Квалификационные и валидационные испытания установок автоматизированного (механизированного) ультразвукового контроля (АУЗК / МУЗК) проводят для подтверждения технических характеристик установок и оценки возможности их применения для контроля качества сварных соединений на конкретном проекте.
20/03/2023 Далее
Можем ли мы вам помочь в решении вашей задачи?
Свяжитесь с нами и задайте свой вопрос. Наши специалисты постараются вам помочь и ответят вам при первой возможности.