Технология проведения квалификационных испытаний средств неразрушающего контроля. Классификация средств ультразвукового контроля
- 12/09/2015
- Опубликовано: rudymore
- Категория: Статьи
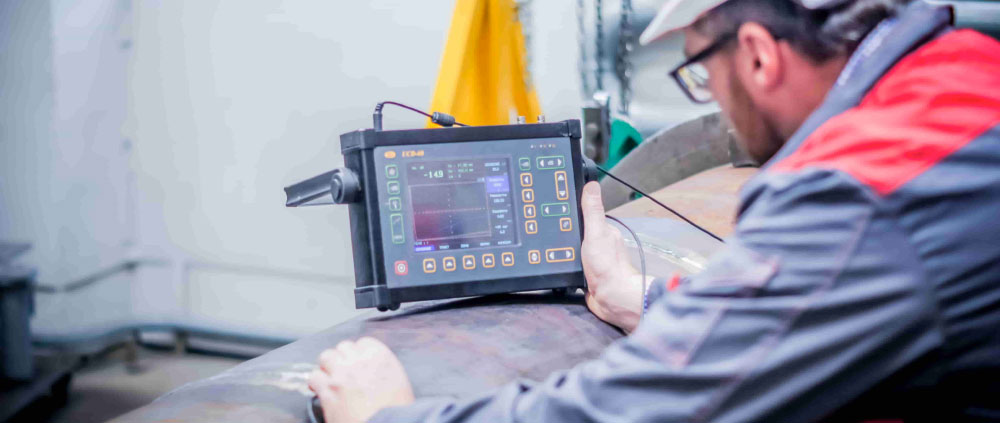
Окунев Д.В., Литвинов И.П. (ООО НИИЦ СТНК “Спектр”), Тульский М.П. (ПАО “Газпром”)
В статье описана технология проведения квалификационных испытаний средств неразрушаю-щего контроля стыковых кольцевых сварных соединений трубопроводов позволяющая снизить стоимость испытаний и сократить их сроки. Предложена система классификации установок ультра-звукового контроля по функциональным возможностям. Материалы подготовлены на основе ре-зультатов проведения в 2014 г. квалификационных испытаний установок неразрушающего контроля.
Статья опубликована в журналах «Технологии НК» (NDT World, 2015, v. 18, no. 4, pp.) и «Территория НефтеГаз» №12 2015 (УДК 620.1:622.69)
Ключевые слова: ультразвуковой контроль, квалификационные испытания АУЗК, валидационные испытания АУЗК, трубы, сварные швы, модель дефекта, рентгеновская томография, система классификации установок УЗК.
Procedure of NDT Instruments Qualification Tests. Classification of Ultrasonic Testing Devices1.
M. Yu. Tulskiy, D. V. Okunev, I. G. Litvinov
Introduction. Qualification tests are carried out with the aim to understand real possibilities of NDT instruments to detect defects as well as calculate measurement errors at size measurements.
Method. Previous experience has shown that it is impossible to obtain defects with given parameters only by changing welding conditions. Defects were made mechanically or with electroerosive method. Size measurements were fulfilled with X-Ray tomograph; its measurement accuracy was confirmed by the results of metallographic study.
Results.18 types of UT instruments have been tested on 5 types of weld grooving. Tests were fulfilled in accordance with DNV-OS-F-101 and DNV-RP-F118 standards. Welds’ unfoldings with indications of detected defects have been presented as well as average values and dispersion of absolute errors of defect parameters measuring. Classifications of UT instruments have been proposed – according to testing hardware implementation and to the methodology of ultrasound application. The results of NDT instruments qualification tests fulfilled in 2014 were used as the basis.
Conclusions. The fulfilled tests have made it possible to determine acceptability of each instrument for pipelines construction and repair.
Keywords: ultrasonic testing, AUT qualification, AUT validation, pipes, welds, model of a defect, X-Ray tomography, UT units’ classification system
Предисловие 2022 года
В 2013 коллектив авторов ООО НИПИСтройТЭК (в 2016 г предприятие переименовано в ООО «НИИЦ СТНК «Спектр») по заданию ОАО «ГазПром» разработал «Временные требования к организации сварочно-монтажных работ, применяемым технологиям сварки, неразрушающему контролю качества сварных соединений и оснащенности подрядных организаций при строительстве, реконструкции и капитальном ремонте магистральных газопроводов ОАО «Газпром». В части неразрушающего контроля данный документ дополнял морально устаревший СТО Газпром 2-2.4-083-2006 «Инструкция по неразрушающим методам контроля качества сварных соединений при строительстве и ремонте промысловых и магистральных газопроводов».
«Временные требования …» легализовали применение систем автоматизированного (АУЗК) и механизированного (МУЗК) ультразвукового контроля с применением преобразователей на фазированных решетках и технологии TOFD. Введение в промышленный обиход средств АУЗК (МУЗК) потребовало проведения квалификационных испытаний всех типов установок АУЗК применяемых или планируемых к применению на территории РФ. Испытания продемонстрировали реальные возможности установок контроля, результаты испытаний послужили основой для выработки рекомендации по применению средств АУЗК. Следует отметить, что выполнение гигантского объема работ на испытаниях в течение 6-7 месяцев и в рамках отведенного нам бюджета стало возможным только благодаря применению предложенной Тульским М.Ю. принципиально новой технологий измерения реальных размеров методом радиационной томографии вместо традиционной металлографии. В настоящее время томография применяется при проведении практически на всех испытаний установок АУЗК. Методы изготовления искусственных дефектов существенно доработаны.
Наше предприятие накопило богатый опыт проведения испытаний установок АУЗК, до 2022 г включительно выполнены следующие работы:
- 2011 г валидационные испытания на проекте Сахалин-1 (заказчик – ОАО «МРТС»);
- 2014 г. квалификационные испытания установок АУЗК и МУЗК (заказчик – ОАО «Газпром»);
- 2014 г. квалификационные испытания установок АУЗК и МУЗК (заказчик – АО «АК «Транснефть»);
- 2017 г. валидационные испытания на проекте SouthStream;
- 2019 г. валидация установки RotoScan для проекта газопровода внешнего транспорта с Новопортовского НГКМ через Обскую губу (заказчик ОАО «МРТС»);
- 2021 г. валидация установки RotoScan для проекта «Обустройство Киринского месторождения» (заказчик ОАО «СуперСтрой XXI»);
- 2022 г валидация установки RotoScan для проекта Обустройство месторождения им. В.И. Грайфера (1-ая стадия освоения). Межпромысловые трубопроводы ЛСП месторождения им. В.И. Грайфера – ЛСП-2 месторождения им. В. Филановского (многофазный трубопровод, трубопровод газлифта, водовод (заказчик – OOO «Лукойл-Нижневолжскнефть»);
- 2022 г валидация установки RotoScan для проекта «Освоение месторождения D33 с объектами инфраструктуры» (заказчик – СуперСтрой XXI)
В июле 2023 г вступят в силу стандарты 2, разработанные ООО «НИИЦ СТНК «Спектр» и АО «ВНИИГаз» на основе «Временных требований …». Публикация этих документов первоначально была намечена на 2019 г, но по независящим от нас обстоятельствам отложена на неопределенное время.
Задачей квалификационных испытаний является определение реальных возможностей установок неразрушающего контроля (далее –НК) по выявлению дефектов, расчёт ошибок измерения размеров дефектов.
В основе программы квалификационных испытаний лежат требования документов [1], [2]. Обработка данных выполняется с учётом рекомендаций [3], [4], [5].
Испытания должны включать следующие этапы:
- изготовление контрольных сварных соединений (КСС);
- изготовление калибровочных блоков для настройки установок;
- предварительный контроль КСС радиографическим методом;
- контроль КСС установками УЗК с документированием результатов;
- выполнение тестов, подтверждающих работоспособность установок контроля (тест на повторяемость результатов, проверка влияния температуры сварного шва на чувствительность УЗК, проверка качества акустического контакта);
- измерение реальных размеров несплошностей в сварном шве;
- определение точности оценки параметров несплошностей (абсолютные ошибки измерения).
Для того, чтобы значения абсолютных ошибок измерения были достоверными, количество дефектов в различных зонах сварного должно соответствовать требованиям таблицы 1.
Каждая зона сварного шва должна содержать характерные для используемого метода сварки допустимые и недопустимые дефекты, дефекты искусственного (~70% общего числа дефектов) и естественного происхождения (~30%). Расстояния между дефектами должны превышать 20-25 мм, что бы при анализе их можно было бы корректно измерить. В облицовочный слой включаются дефекты, лежащие на глубине до 5 мм от поверхности.
По результатам предварительного РК и томографии рекомендуется убрать из рассмотрения дефекты, перекрывающие друг- друга в вертикальном или горизонтальном сечениях шва, так как они могут быть некорректно измерены методом УЗК.
Для измерения реальных размеров дефектов нормативная документация [1] рекомендует металлографический метод исследования (метод «салями»), при котором дефектная зона нарезается на шлифы. Высота дефекта, выходящего на шлиф, должна измеряться с точностью ±0,1 мм, при этом точность измерения протяжённости зависит от шага выполнения шлифов. Данный метод весьма трудозатратен, его применение делает невозможным оперативное выполнение больших объёмов работ. Проблему решает применение радиационной томографии.
Для изготовления дефектов необходимо подготовить карту расположения дефектов с указанием номеров сварочных слоёв, типов и параметров закладываемых дефектов.
Предыдущий опыт проведения квалификационных испытаний показал, что получить дефекты с заданными параметрами изменением режимов сварки невозможно, кроме того, данный способ не позволяет получить дефекты с высотой менее высоты сварочного слоя и протяжённостью менее 10-12 мм. Вваривание пластин из неплавящихся материалов в сварочную ванну трудноосуществимо.
Наиболее эффективным способом изготовления дефектов является механический способ.
Плоскостные дефекты по разделке кромок и имитаторы трещин изготавливаются с помощью фрезы из спечённых алмазных дисков или электроэрозионным способом. В полученный пропил (паз) шириной 0,4 – 0,5 мм укладывается твердосплавная пластина, верхний край пропила закернивается. Опыт квалификационных испытаний показал, что можно обойтись и без твердосплавных пластин – расплавленный металл, как правило, не заливает пазы.
Дефекты типа пор и скоплений имитируются высверливанием и последующим закерниванием отверстий.
Следует учесть, что при изготовлении внутренних дефектов механическим способом невозможно получить несплошность точно заданного размера. Протяжённость и высота искусственного отражателя определяется глубиной проплавления верхней кромки паза, глубиной фрезеровки и диаметром фрезы. Газы, поднимающиеся из паза при заварке дефекта, могут создать скопление пор или вертикальный воронкообразный газовый канал над дефектом и изменить его геометрию (см. Рисунок 1).
Рисунок 1 – Размеры реальных несплошностей не совпадают с размерами твердосплавных пла-стинок, пазов и сверлений, использованных для изготовления дефектов
Электроэрозионное изготовление внутренних дефектов требует большего времени, но даёт более предсказуемые результаты по протяжённости и высоте дефектов чем изготовление фрезерованием. Данный метод лучше использовать для изготовления имитаторов дефектов, расположенных в нижних слоях шва, где использование фрезы невозможно и поверхностных дефектов: подрезов, непроваров в корне шва, трещин в облицовке шва, несплавлений, выходящих на поверхность.
Томографическая установка GE v|tome|x m300 (производство компании GE Sensing & Inspection Technologes GmbH), выбранная для проведения измерения размеров дефектов сварного шва, даёт возможность регистрировать дефекты объёмом от 0,1 мм3, различать детали изображения размером от 0,5 – 1 мкм.
Для проведения томографического исследования из сварного шва вырезаются темплеты длиной 400-420 мм и шириной 25-26 мм. При проведении радиационной томографии необходимо правильно выбрать минимальный регистрируемый и индицируемый объёмы несплошности, шаг поворота объекта при просвечивании. Данные параметры влияют не только на количество выявленных дефектов, но и на время сканирования и, следовательно, стоимость исследования. Уменьшение объёма регистрируемых дефектов ведёт к появлению помех и избыточного количества информации. Так, при установке регистрируемого объёма равного 0,3 мм3 было получено около 7 тысяч индикаций в кольцевом шве трубы 1420х26. При увеличении объёма до 0,8 мм3 полученное количество индикаций стало примерно соответствовать количеству индикаций, зарегистрированных установками АУЗК (90-120 индикаций в шве).
Точность измерений, выполненных томографической установкой, подтверждена данными металлографии. Расхождение результатов измерения линейных размеров данными методами составило 7,7 ±8,7 мкм, а по глубине залегания 103,6 ± 47,6 мкм, что примерно соответствует предельной точности измерения при металлографическом исследовании шлифов.
Сравнение стоимостных характеристик металлографического и томографического контроля (см. Таблицы 2 и 3) показывает почти пятикратное преимущество томографического метода по производительности и пятидесятикратное по стоимости. Увеличение количества анализируемых дефектов увеличивает стоимость металлографического исследования и практически не сказывается на стоимости томографии.
Использование томографического метода позволяет выполнить проверку результатов измерений и корректировку параметров индикаций дефектов, сделать исследование более точным. Результаты томографии могут быть использованы для корректировки чувствительности УЗК.
Время сканирования темплета длиной 400-410 мм, ч | 4-5 |
Время обработки данных сканирования темплета длиной 400-410 мм, ч | 3-4 |
Общая протяжённость шва, обработанного за сутки, мм | 1200 |
Количество дефектов, обработанных за сутки, шт | 27-32 |
Стоимость обработки одного дефекта, усл. ед | 10-12 |
Минимальное количество шлифов на 1 дефект | 10 |
Максимальное количество шлифов, выполненных за сутки, шт | 18-22 |
Количество дефектов, обработанных за сутки, шт | 2–2,2 |
Стоимость обработки одного дефекта, усл. ед. | 400-500 |
В ходе испытаний установок НК должны измеряться: протяжённость, высота и глубина залегания дефектов. Для установок, выполняющих разбраковку по амплитудному критерию, – протяжённость, глубина залегания и амплитуда эхо-сигнала.
В соответствии с требованиями нормативной документации ОАО «Газпром» глубина залегания дефекта не входит в перечень критериев разбраковки сварного шва, но её точное измерение обязательно для установок, применяемых при строительстве и капитальном ремонте. Знание этого параметра позволяет отрегулировать режимы сварочной установки для конкретного сварочного слоя.
На основании анализа данных томографии и результатов контроля КСС, полученных установкой НК вычисляется среднее значение и дисперсия абсолютных ошибок измерения параметров дефекта. Для облегчения анализа результатов строится развёртка сварного шва с индикациями обнаруженных дефектов (Рисунок 2), графики расхождения результатов НК и томографии (Рисунок 3). По гистограммам распределения значений абсолютных ошибок можно сравнить точность оценки параметров дефектов различными установками НК. Построение гистограммы распределения обнаруженных несплошностей по глубине сварного шва (Рисунок 5) позволяет определить допустимость применения установки при строительстве и капитальном ремонте трубопроводов.
Рисунок 5 – Гистограммы распределения обнаруженных дефектов по глубине контрольных сварных соеди-нений
Значения ошибок измерения дефектов должны учитываться при выработке индивидуаль-ных критериев разбраковки для каждой установки НК. Критерии разрабатываются на основе инженерной оценки допустимых дефектов для конкретного типа трубы и участка прокладки трубопровода. Рисунок 6 иллюстрирует преимущества применения установок НК с более точ-ными показателями измерения размеров дефектов. На графике изображены границы областей допустимых дефектов для кольцевого сварного шва трубы (базовая характеристика) и двух установок УЗК. Выше границ находится область недопустимых значений параметров дефектов. Критерии для установок УЗК получают вычитанием ошибок измерения дефектов из базовой характеристики. Размеры допустимых дефектов для установки УЗК1 с меньшими значениями ошибок почти в два раза превышают допустимые размеры для установки УЗК2. Это означает, что количество дефектов, идентифицированных как недопустимые по результатам контроля бо-лее точной установкой НК, будет меньше, а затраты на ремонт сварных швов – ниже.
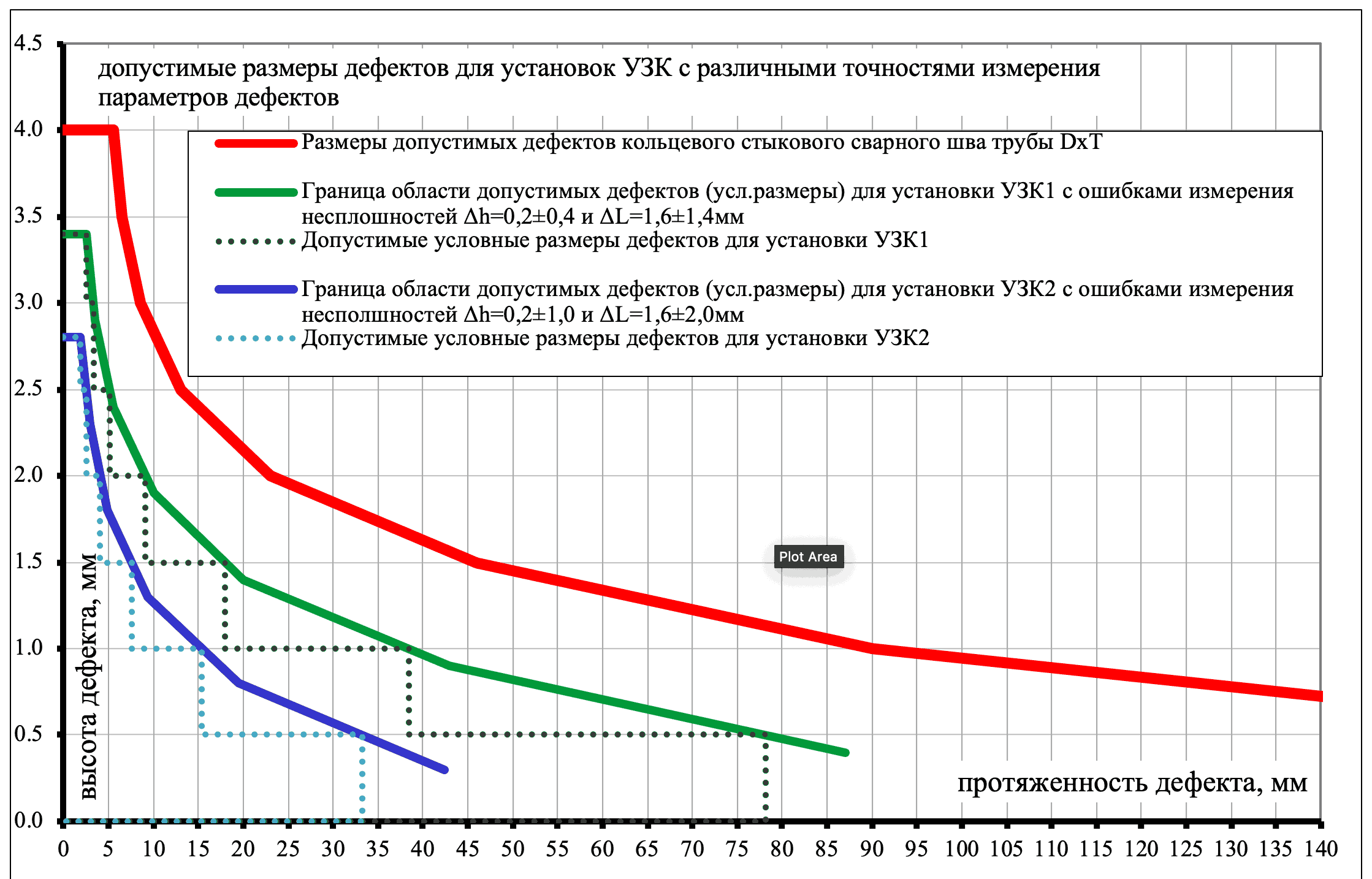
Допустимость применения установки УЗК для контроля конкретной разделки сварного шва должна определяться по результатам квалификационных испытаний. Схемы контроля, реализу-емые установками УЗК, должны классифицироваться по аппаратной реализации контроля и ме-тодологии применения ультразвука. Нормативная документация должна содержать требования к допустимости применения установок определённого класса для контроля конкретных типов сварных соединений. Функциональные возможности установок предлагается описывать циф-робуквенным кодом[1].
1 | Контроль с использованием одного акустического канала[2]. Параметры излучаемого сигнала не изменяются в ходе контроля. Запись результатов контроля выполняется вручную в от-дельных точках контролируемого объекта |
2 | Контроль с использованием нескольких акустических каналов. Параметры каналов не изме-няются в ходе контроля. Запись результатов контроля выполняется автоматически по всему проконтролированному объекту |
3 | Контроль с использованием фазированных решёток. При контроле применяется физическая фокусировка УЗ-луча, динамическое изменение схем прозвучивания в зависимости от пара-метров разделки сварного шва, может использоваться секторное сканирование, линейное сканирование под несколькими углами. Запись результатов контроля выполняется автомати-чески по всему проконтролированному объёму |
4 | Контроль с использованием антенных решёток. При контроле применяется программная (ма-тематическая) фокусировка УЗ-луча. Запись результатов контроля выполняется автоматиче-ски по всему проконтролированному объёму |
Примечания
1 Статья опубликована в 2015 г журналах «В мире НК» (NDT World, 2015, v.18, no.4) и «Территория НефтеГаз» № 12 декабрь 2015, УДК 620.1:622.69)
2 СТО Газпром 15-1.1-002-2019 Сварка и неразрушающий контроль сварных соединений. технологии сварки промысловых и магистральных газопроводов
СТО Газпром 15-1.3-004-2019 Сварка и неразрушающий контроль сварных соединений. Неразрушающие методы контроля качества сварных соединений промысловых и магистральных газопроводов
СТО Газпром 15–1.5–006–2019 Сварка и неразрушающий контроль сварных соединений. Требования к организации сварочно–монтажных работ, применяемым технологиям сварки и неразрушающему контролю качества сварных соединений при строительстве, реконструкции и капитальном ремонте магистральных газопроводов
[1] Установки УЗК дают возможность гибкой перенастройки параметров контроля, поэтому конкретная установка может иметь несколько классов обозначений
[2] Акустический канал характеризуется следующими параметрами: направлением излучения, типом излучаемой волны, параметрами фокусировки излучения
[3] При зональном методе контроля поверхность разделки сварного соединения делится по высоте на зоны, приблизительно равные высоте сварочного слоя. Высота зоны горячего прохода и корневой зоны устанавливаются в соответствии с параметрами разделки сварного шва. Зона заполнения сварного шва делится на зоны, высота которых зависит от толщины контролируемого соединения. Для каждой зоны контроля формируется индивидуальная совмещенная или тандемная схема прозвучивания, которая зависит от угла разделки кромок и условий выявления дефектов. Деление разделки на зоны позволяет осуществлять оперативную регулировку параметров сварочных головок при обнаружении дефектов.
[4] TOFD: метод ультразвукового контроля (Time-of-Flight Difraction), выполняемого в соответствии с требованиями стандартов ISO 16826, ISO 10863
Список литературы
- DNV-OS-F-101 Submarine Pipeline Systems. Offshore Standard.
- DNV-RP-F118 Pipe Girth weld AUT system qualification and project specific procedure validation. Recommended Practice.
- NT Techn Report 394 Guidelines for NDE Reliability Determination and Description.
- NT TR 427. Guidelines for Development of NDE Acceptance Criteria. Nordtest Technical Report
- MIL-HDBK-1823A. Nondestructive evaluation system reliability assessment. (7 April 2009)
-
Технология ультразвукового контроля сварных соединений стенки стальных вертикальных резервуаров без удаления защитного лакокрасочного покрытия
В статье описана технология проведения квалификационных испытаний средств неразрушаю-щего контроля стыковых кольцевых сварных соединений трубопроводов позволяющая снизить стоимость испытаний и сократить их сроки. Предложена система классификации установок ультра-звукового контроля по функциональным возможностям.
02/10/2008 Далее -
Технология проведения квалификационных испытаний средств неразрушающего контроля. Классификация средств ультразвукового контроля
Задачей квалификационных испытаний является определение реальных возможностей установок неразрушающего контроля (далее –НК) по выявлению дефектов, расчёт ошибок измерения размеров дефектов
12/09/2015 Далее -
Оценка результатов валидации установок АУЗК
Квалификационные и валидационные испытания установок автоматизированного (механизированного) ультразвукового контроля (АУЗК / МУЗК) проводят для подтверждения технических характеристик установок и оценки возможности их применения для контроля качества сварных соединений на конкретном проекте.
20/03/2023 Далее
Можем ли мы вам помочь в решении вашей задачи?
Свяжитесь с нами и задайте свой вопрос. Наши специалисты постараются вам помочь и ответят вам при первой возможности.